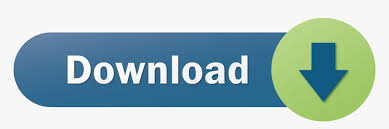
3D Exploration 1.833 serial key or number

3D Exploration 1.833 serial key or number
Saturn V
The launch of Apollo 11 on Saturn V SA, July 16, | |
Function | |
---|---|
Manufacturer | |
Country of origin | United States |
Project cost | $ billion in – dollars[1] (~$ billion in dollars) |
Cost per launch | $ million in – dollars[2] ($ billion in value). |
Size | |
Height | ft (m) |
Diameter | ft (m) |
Mass | 6,,lb (2,,kg)[3] |
Stages | 2–3 |
Capacity | |
Payload to LEO | |
Altitude | 90nmi (km) |
Inclination | 30° |
Mass | ,lb (,kg)[4][5][note 1] |
Payload to TLI | |
Mass | ,lb (48,kg)[3] |
Associated rockets | |
Family | Saturn |
Derivatives | Saturn INT |
Comparable | |
Launch history | |
Status | Retired |
Launch sites | LC, Kennedy Space Center |
Total launches | 13 |
Success(es) | 12 |
Failure(s) | 0 |
Partial failure(s) | 1 (Apollo 6) |
First flight | November 9, (AS[note 2]Apollo 4) [6] |
Last flight | May 14, (AS Skylab) [7] |
First stage – S-IC | |
Length | ft (m) |
Diameter | ft (m) |
Empty mass | ,lb (,kg) |
Gross mass | 5,,lb (2,,kg) |
Engines | 5 Rocketdyne F-1 |
Thrust | 7,,lbf (35,kN) sea level |
Specific impulse | seconds (km/s) sea level |
Burn time | seconds |
Fuel | RP-1 / LOX |
Second stage – S-II | |
Length | ft (m) |
Diameter | ft (m) |
Empty mass | 88,lb (40,kg)[note 3] |
Gross mass | 1,,lb (,kg)[note 3] |
Engines | 5 Rocketdyne J-2 |
Thrust | 1,,lbf (5,kN) vacuum |
Specific impulse | seconds (km/s) vacuum |
Burn time | seconds |
Fuel | LH2 / LOX |
Third stage – S-IVB | |
Length | ft (m) |
Diameter | ft (m) |
Empty mass | 33,lb (15,kg)[8][note 4] |
Gross mass | ,lb (,kg)[note 4] |
Engines | 1 Rocketdyne J-2 |
Thrust | ,lbf (1,kN) vacuum |
Specific impulse | seconds (km/s) vacuum |
Burn time | + seconds (2 burns) |
Fuel | LH2 / LOX |
Saturn V was an American super heavy-lift launch vehicle certified for human-rating used by NASA between and It consisted of three stages, each fueled by liquid propellants. It was developed to support the Apollo program for human exploration of the Moon and was later used to launch Skylab, the first American space station.
The Saturn V was launched 13 times from Kennedy Space Center with no loss of crew or payload. As of ,[update] the Saturn V remains the tallest, heaviest, and most powerful (highest total impulse) rocket ever brought to operational status, and holds records for the heaviest payload launched and largest payload capacity to low Earth orbit (LEO) of ,lb (,kg), which included the third stage and unburned propellant needed to send the Apollo command and service module and Lunar Module to the Moon.
As the largest production model of the Saturn family of rockets, the Saturn V was designed under the direction of Wernher von Braun at the Marshall Space Flight Center in Huntsville, Alabama, with Boeing, North American Aviation, Douglas Aircraft Company, and IBM as the lead contractors.
To date[update], the Saturn V remains the only launch vehicle to carry humans beyond low Earth orbit. A total of 15 flight-capable vehicles were built, but only 13 were flown. An additional three vehicles were built for ground testing purposes. A total of 24 astronauts were launched to the Moon in the four years spanning December through December
History[edit]
In September ,[9] the US government brought the German rocket technologist Wernher von Braun and about seven hundred German rocket engineers and technicians to the United States for Operation Paperclip,[10][11] a program authorized by President Truman.[12]
Von Braun was assigned to the Army's rocket design division due to his prior direct involvement in the creation of the V-2 rocket.[13] Between and , his work was restricted to conveying the ideas and methods behind the V-2 to American engineers.[14] Despite von Braun's many articles on the future of space rocketry,[15] the US government continued funding Air Force and Navy rocket programs to test their Vanguard missiles despite numerous costly failures.[16]
The US Army and government began taking serious steps towards sending Americans into space in , when the Soviets launched Sputnik 1 atop an R-7 ICBM, which is capable of carrying a thermonuclear warhead to the US.[17][18][19] They turned to von Braun's team, who had created and experimented with the Jupiter series of rockets. [20]
The Juno I rocket launched the first American satellite in January ,[21] and was part of the last-ditch plan for NACA (the predecessor of NASA) to participate in the Space Race.[22] Von Braun considered the Jupiter series to be a prototype and referred to it as "an infant Saturn".[19]
Saturn development[edit]
The Saturn program was named for the next planet after Jupiter. Its design stemmed from the designs of the Jupiter series rockets. As the success of the Jupiter series became evident, the Saturn series emerged.[23] Between and , the Marshall Space Flight Center (MSFC) designed a series of Saturn rockets that could be deployed for various Earth orbit or lunar missions.[24]
NASA planned to use the Saturn C-3 as part of the Earth orbit rendezvous (EOR) method, with at least four or five launches needed for a single lunar mission.[25]. However, the MSFC planned an even bigger rocket, the C-4, which would use four F-1 engines in its first stage, an enlarged C-3 second stage, and the S-IVB, a stage with a single J-2 engine, as its third stage. The C-4 would need only two launches to carry out an EOR lunar mission.[26]
On January 10, , NASA announced plans to build the C The three-stage rocket would consist of: the S-IC first stage, with five F-1 engines; the S-II second stage, with five J-2 engines; and the S-IVB third stage, with a single J-2 engine.[27] The C-5 was designed for a 90,pound (41,kg) payload capacity to the Moon.[27]
The C-5 would undergo component testing even before the first model was constructed. The S-IVB third stage would be used as the second stage for the C-IB, which would serve both to demonstrate proof of concept and feasibility for the C-5, but would also provide flight data critical to development of the C[27] Rather than undergoing testing for each major component, the C-5 would be tested in an "all-up" fashion, meaning that the first test flight of the rocket would include complete versions of all three stages. By testing all components at once, far fewer test flights would be required before a crewed launch.[28]
The C-5 was confirmed as NASA's choice for the Apollo program in early , and was named the SaturnV.[27] The C-1 became the Saturn I, and C-1B became Saturn IB. Von Braun headed a team at the MSFC to build a vehicle capable of launching a crewed spacecraft to the Moon.[19]
Before they moved under NASA's jurisdiction, von Braun's team had already begun work on improving the thrust, creating a less complex operating system, and designing better mechanical systems.[19] During these revisions, the team rejected the single engine of the V-2's design and moved to a multiple-engine design. The Saturn I and IB reflected these changes but were not large enough to send a crewed spacecraft to the Moon.[19] These designs, however, provided a basis for which NASA could determine its best method towards landing a man on the Moon.[19]
The Saturn V's final design had several key features. Engineers determined that the best engines were the F-1s coupled with the new liquid hydrogen propulsion system called J-2, which made the Saturn C-5 configuration optimal.[19] By , NASA had finalized its plans to proceed with von Braun's Saturn designs, and the Apollo space program gained speed.[29]
With the configuration finalized, NASA turned its attention to mission profiles. Despite some controversy, a lunar orbit rendezvous for the lunar module was chosen over an Earth orbital rendezvous.[19] Issues such as type of fuel injections, the amount of fuel needed for the trip, and rocket manufacturing processes were resolved, and the designs for the Saturn V were selected. The stages were designed by von Braun's Marshall Space Flight Center in Huntsville, and outside contractors were chosen for the construction: Boeing (S-IC), North American Aviation (S-II), Douglas Aircraft (S-IVB), and IBM (instrument unit).[29]
Selection for Apollo lunar landing[edit]
Early in the planning process, NASA considered three methods for the Moon mission: Earth orbit rendezvous (EOR), direct ascent, and lunar orbit rendezvous (LOR). A direct ascent configuration would require an extremely large rocket to send a three-man spacecraft to land directly on the lunar surface. An EOR would launch the direct-landing spacecraft in two smaller parts which would combine in Earth orbit. A LOR mission would involve a single rocket launching two spacecraft: a mother ship, and a smaller, two-man landing module which would rendezvous back with the main spacecraft in lunar orbit. The lander would be discarded and the mother ship would return home.[30]
At first, NASA dismissed LOR as a riskier option, as a space rendezvous had yet to be performed in Earth orbit, much less in lunar orbit. Several NASA officials, including Langley Research Center engineer John Houbolt and NASA Administrator George Low, argued that a lunar orbit rendezvous provided the simplest landing on the Moon with the most cost–efficient launch vehicle, and the best chance to accomplish the lunar landing within the decade.[27] Other NASA officials were convinced, and LOR was officially selected as the mission configuration for the Apollo program on November 7, [27]Arthur Rudolph became the project director of the Saturn V rocket program in August He developed the requirements for the rocket system and the mission plan for the Apollo program. The first Saturn V launch lifted off from Kennedy Space Center and performed flawlessly on November 9, , Rudolph's birthday.[31] He was then assigned as the special assistant to the director of MSFC in May and subsequently retired from NASA on January 1, [32] During his tenure he was awarded the NASA Exceptional Service Medal and the NASA Distinguished Service Medal. On July 16, , the Saturn V launched Apollo 11, putting man on the Moon. [33]
Technology[edit]
The Saturn V's size and payload capacity dwarfed all other previous rockets successfully flown at that time. With the Apollo spacecraft on top, it stood feet (m) tall, and, ignoring the fins, was 33 feet (10m) in diameter. Fully fueled, the Saturn V weighed million pounds (2,,kg)[3] and had a low Earth orbit payload capacity originally estimated at , pounds (,kg), but was designed to send at least 90, pounds (41,kg) to the Moon.[34]
Later upgrades increased that capacity; during the final three Apollo lunar missions it deployed about , pounds (,kg)[4][5][note 1] to LEO and sent up to ,lb (48,kg)[3] spacecraft to the Moon. At a height of feet (m), the Saturn V was 58 feet (18m) taller than the Statue of Liberty from the ground to the torch, and 48 feet (15m) taller than the Big Ben clock tower.[35]
In contrast, the Mercury-Redstone Launch Vehicle used on Freedom 7, the first crewed American spaceflight, was approximately 11 feet (m) longer than the S-IVB stage and delivered less sea level thrust (78, pounds-force (kN))[36] than the Launch Escape System rocket (, pounds-force (kN) sea level thrust) mounted atop the Apollo command module.[37]The Apollo LES fired for a much shorter time than the Mercury-Redstone ( seconds vs. seconds)[36][37].
The Saturn V was principally designed by the Marshall Space Flight Center in Huntsville, Alabama, although numerous major systems, including propulsion, were designed by subcontractors. It used the powerful F-1 and J-2rocket engines for propulsion, which shattered the windows of nearby houses when they were tested at Stennis Space Center.[38] Designers decided early on to attempt to use as much technology from the Saturn I program as possible. Consequently, the S-IVB third stage of the Saturn V was based on the S-IVB second stage of the Saturn IB. The instrument unit that controlled the Saturn V shared characteristics with the one carried by the Saturn IB.[39]
The Saturn V was primarily constructed of aluminum. It was also made of titanium, polyurethane, cork and asbestos.[40] Blueprints and other Saturn V plans are available on microfilm at the Marshall Space Flight Center.[41]
Stages[edit]
The Saturn V consisted of three stages—the S-IC first stage, S-II second stage and the S-IVB third stage—and the instrument unit. All three stages used liquid oxygen (LOX) as the oxidizer. The first stage used RP-1 for fuel, while the second and third stages used liquid hydrogen (LH2). Whereas LH2 has a much higher energy density to be lifted into orbit by mass, RP-1 has a much higher energy density by volume. Consequently, RP-1 was chosen for the first stage propellant because the volume of LH2 required would have been more than three times greater and would have created much higher aerodynamic drag during the boost phase through the atmosphere.[42] The upper stages also used small solid-propellant ullage motors that helped to separate the stages during the launch, and to ensure that the liquid propellants were in a proper position to be drawn into the pumps.[43]
S-IC first stage[edit]
The S-IC was built by the Boeing Company at the Michoud Assembly Facility, New Orleans, where the Space Shuttle external tanks would later be built by Lockheed Martin. Most of its mass at launch was propellant: RP-1 fuel with liquid oxygen as the oxidizer.[44] It was feet (42m) tall and 33 feet (10m) in diameter, and provided over 7,, pounds-force (34,kN) of thrust. The S-IC stage had a dry weight of about , pounds (, kilograms); when fully fueled at launch, it had a total weight of 5,, pounds (2,, kilograms). It was powered by five Rocketdyne F-1 engines arrayed in a quincunx. The center engine was held in a fixed position, while the four outer engines could be hydraulically turned with gimbals to steer the rocket.[44] In flight, the center engine was turned off about 26 seconds earlier than the outboard engines to limit acceleration. During launch, the S-IC fired its engines for seconds (ignition occurred about seconds before liftoff) and at engine cutoff, the vehicle was at an altitude of about 42 miles (67km), was downrange about 58 miles (93km), and was moving about 7, feet per second (2,m/s).[45]
S-II second stage[edit]
The S-II was built by North American Aviation at Seal Beach, California. Using liquid hydrogen and liquid oxygen, it had five Rocketdyne J-2 engines in a similar arrangement to the S-IC, also using the outer engines for control. The S-II was feet (m) tall with a diameter of 33 feet (10m), identical to the S-IC,[46][47] and thus was the largest cryogenic stage until the launch of the Space Shuttle in The S-II had a dry weight of about 80, pounds (36,kg); when fully fueled, it weighed 1,, pounds (,kg). The second stage accelerated the Saturn V through the upper atmosphere with 1,, pounds-force (4,kN) of thrust in a vacuum.[48]
When loaded, significantly more than 90 percent of the mass of the stage was propellant; however, the ultra-lightweight design had led to two failures in structural testing. Instead of having an intertank structure to separate the two fuel tanks as was done in the S-IC, the S-II used a common bulkhead that was constructed from both the top of the LOX tank and bottom of the LH2 tank. It consisted of two aluminum sheets separated by a honeycomb structure made of phenolic resin.[49][50] This bulkhead had to insulate against the °F (52°C) temperature difference between the two tanks. The use of a common bulkhead saved 7, pounds (t) by both eliminating one bulkhead and reducing the stage's length.[51] Like the S-IC, the S-II was transported from its manufacturing plant to the Cape by sea. [52]
S-IVB third stage[edit]
The S-IVB was built by the Douglas Aircraft Company at Huntington Beach, California. It had one J-2 engine and used the same fuel as the S-II. The S-IVB used a common bulkhead to separate the two tanks. It was feet (m) tall with a diameter of feet (m) and was also designed with high mass efficiency, though not quite as aggressively as the S-II. The S-IVB had a dry weight of about 23, pounds (10,kg) and, fully fueled, weighed about , pounds (,kg).[53]
The S-IVB was the only rocket stage of the Saturn V small enough to be transported by Aero Spacelines Pregnant Guppy. [54]
Instrument unit[edit]
The instrument unit was built by IBM and was placed on top of the third stage. It was constructed at the Space Systems Center in Huntsville, Alabama. This computer controlled the operations of the rocket from just before liftoff until the S-IVB was discarded. It included guidance and telemetry systems for the rocket. By measuring the acceleration and vehicle attitude, it could calculate the position and velocity of the rocket and correct for any deviations.[55]
Range safety[edit]
In the event of an abort requiring the destruction of the rocket, the range safety officer would remotely shut down the engines and after several seconds send another command for the shaped explosive charges attached to the outer surfaces of the rocket to detonate. These would make cuts in fuel and oxidizer tanks to disperse the fuel quickly and to minimize mixing. The pause between these actions would give time for the crew to escape via the Launch Escape Tower or (in the later stages of the flight) the propulsion system of the Service module. A third command, "safe", was used after the S-IVB stage reached orbit to irreversibly deactivate the self-destruct system. The system was inactive as long as the rocket was still on the launch pad.[56]
Comparisons[edit]
Titan II[edit]
The Saturn V had a much lower thrust-to-weight ratio than Titan II GLV, the launch system used by Project Gemini, NASA's second human spaceflight program. Richard F. Gordon, Jr. described Saturn V as "an old man's ride", with "a lot more shake-rattle-and-roll" but milder thrust. Buzz Aldrin and other Apollo 11 astronauts agreed that unlike Titan, they could not tell when Saturn V liftoff occurred except from instruments.[57]
Soviet N1-L3[edit]
The Soviet space program's counterpart to the Saturn V was Sergei Korolev's N1-L3. The Saturn V was taller, heavier, and had a greater payload capacity, both to low Earth orbit and to translunar injection.[58] The N-1 was a three-stage launch vehicle with more liftoff thrust and a larger first stage diameter than the Saturn V. It was to carry the ,lb (95,kg) L3 vehicle into orbit.[59][60]
The N1 never became operational; each of its four test launches resulted in catastrophic vehicle failure early in flight, and the program was canceled.[61] Korolev elected to cluster 30 relatively small engines for the first stage, rather than develop a large engine like the Rocketdyne F[62]
The three-stage Saturn V grew over its lifetime to a peak thrust of at least 7,,lbf (34,kN) (AS and subsequent)[63] and a lift capacity of ,lb (,kg) to LEO. The AS mission (Apollo 15) had a liftoff thrust of 7,,lbf (34,kN). The AS mission (Skylab 1) had slightly greater liftoff thrust of 7,,lbf (35,kN). By comparison, the N-1 had a sea-level liftoff thrust of about 10,,lbf (45,kN).[64] No other operational launch vehicle has surpassed the Saturn V in height, weight, total impulse, or payload capability. The closest contenders were the US Space Shuttle, the Soviet Energia, and the Falcon Heavy vehicle, manufactured by SpaceX. [65][66]
Saturn V (Apollo 11)[67] | N1-L3 | |
---|---|---|
Diameter, maximum | 33ft (10m) | 56ft (17m) |
Height w/ payload | ft (m) | ft (m) |
Gross weight | 6,,lb (2,t) | 6,,lb (2,t) |
First stage | S-IC | Block A |
Thrust, SL | 7,,lbf (33,kN) | 10,,lbf (45,kN) |
Burn time, s | ||
Second stage | S-II | Block B |
Thrust, vac | 1,,lbf (5,kN) | 3,,lbf (14,kN) |
Burn time, s | ||
Orbital insertion stage | S-IVB (burn 1) | Block V |
Thrust, vac | ,lbf (kN) | ,lbf (1,kN) |
Burn time, s | ||
Total impulse[68] | ×109lbf (×106kN)·s | ×109lbf (×106kN)·s |
Orbital payload | ,lb (t)[69] | ,lb (95t) |
Injection velocity | 25,ft/s (7,m/s) | 25,ft/s (7,m/s)[70] |
Payload momentum | ×108slug-ft/s (×108kg·m/s) | ×108 slug-ft/s (×108kg·m/s) |
Propulsive efficiency | % | % |
Earth departure stage | S-IVB (burn 2) | Block G |
Thrust, vac | ,lbf (kN) | ,lbf (kN) |
Burn time, s | ||
Total impulse[68] | ×109lbf (×106kN)·s | ×109lbf (×106kN)·s |
Translunar payload | ,lb (t) | 52,lb (t) |
Injection velocity | 35,ft/s (10,m/s) | 35,ft/s (10,m/s)[70] |
Payload momentum | ×108 slug-ft/s (×108kg·m/s) | ×107 slug-ft/s (×108kg·m/s) |
Propulsive efficiency | % | % |
U.S. Space Shuttle[edit]
The Space Shuttle generated a peak thrust of 6,,lbf (30,kN),[71] and payload capacity to LEO (excluding the Orbiter itself) was 63, pounds (28,kg), which was about 25 percent of the Saturn V's payload. Its total mass in orbit, including the Orbiter, was about ,lb (,kg), compared to the Apollo 15 total orbital mass of the S-IVB third stage and Apollo spacecraft's ,lb (,kg), some 62,lb (28,kg) heavier than the Shuttle was rated to carry to LEO.[72]
Soviet Energia/Buran[edit]
Energia had a liftoff thrust of 7,,lbf (34,kN).[73] It flew twice in and , the second time as the launcher for the Buran spacecraft. However, both the Energia and Buran programs were canceled in Hypothetical future versions of Energia might have been significantly more powerful than the Saturn V, delivering 10,,lbf (46,kN) of thrust and being able to deliver up to ,lb (t) to LEO in the "Vulkan" configuration. Planned uprated versions of the Saturn V using F-1A engines would have had about 18 percent more thrust and , pounds (,kg) payload.[74] NASA contemplated building larger members of the Saturn family, such as the Saturn C-8, and also unrelated rockets, such as Nova, but these were never produced.[75]
Space Launch System[edit]
NASA's Space Launch System, planned for its maiden flight in ,[76] is planned to be feet (m) tall with payload in its final configuration, and lift up to , pounds (,kg) into low Earth orbit.[77]
Other vehicles[edit]
Some other recent US launch vehicles have significantly lower launch capacity to LEO than Saturn V: the US Delta IV Heavy's capacity is 63,lb (28,kg),[78] the Atlas V has a capacity of 41,lb (18,kg),[79] and the Falcon Heavy vehicle, manufactured by SpaceX, has the maximum payload capacity of ,lb (63,kg).[80] The European Ariane 5 ES delivers up to 46,lb (21,kg)[81] and the Russian Proton-M can launch 51,lb (23,kg).[82]
Assembly[edit]
After the construction and ground testing of a stage was completed, it was shipped to the Kennedy Space Center. The first two stages were so massive that the only way to transport them was by barge. The S-IC, constructed in New Orleans, was transported down the Mississippi River to the Gulf of Mexico.[83]
After rounding Florida, the stages were transported up the Intra-Coastal Waterway to the Vehicle Assembly Building (originally called the Vertical Assembly Building). This was essentially the same route which would be used later by to ship Space Shuttle external tanks. The S-II was constructed in California and traveled to Florida via the Panama Canal. The third stage and Instrument Unit could be carried by the Aero Spacelines Pregnant Guppy and Super Guppy, but could also have been carried by barge if warranted.[83]
Upon arrival at the Vertical Assembly Building, each stage was inspected in a horizontal position before being oriented vertically. NASA also constructed large spool-shaped structures that could be used in place of stages if a particular stage was delayed. These spools had the same height and mass and contained the same electrical connections as the actual stages.[83]
NASA stacked (assembled) the Saturn V on a Mobile Launcher (ML), which consisted of a Launch Umbilical Tower (LUT) with nine swing arms (including the crew access arm), a "hammerhead" crane, and a water suppression system which was activated prior to launch. After assembly was completed, the entire stack was moved from the Vehicle Assembly Building (VAB) to the launch pad using the Crawler Transporter (CT). Built by the Marion Power Shovel Company (and later used for transporting the smaller and lighter Space Shuttle), the CT ran on four double-tracked treads, each with 57 "shoes". Each shoe weighed 2, pounds (kg). This transporter was also required to keep the rocket level as it traveled the 3 miles (km) to the launch site, especially at the 3 percent grade encountered at the launch pad. The CT also carried the Mobile Service Structure (MSS), which allowed technicians access to the rocket until eight hours before launch, when it was moved to the "halfway" point on the Crawlerway (the junction between the VAB and the two launch pads).[83]
Lunar mission launch sequence[edit]
The Saturn V carried all Apollo lunar missions,[84] which were launched from Launch Complex 39 at the John F. Kennedy Space Center in Florida.[85] After the rocket cleared the launch tower, flight control transferred to Mission Control at the Johnson Space Center in Houston, Texas.[86]
An average mission used the rocket for a total of just 20 minutes. Although Apollo 6 experienced three engine failures,[87] and Apollo 13 one engine shutdown,[88] the onboard computers were able to compensate by burning the remaining engines longer to achieve parking orbit.[89]
S-IC sequence[edit]
The first stage burned for about 2 minutes and 41 seconds, lifting the rocket to an altitude of 42 miles (68km) and a speed of 6, miles per hour (2,m/s) and burning 4,, pounds (2,,kg) of propellant.[90]
At seconds before launch, the first stage ignition sequence started. The center engine ignited first, followed by opposing outboard pairs at millisecond intervals to reduce the structural loads on the rocket. When thrust had been confirmed by the onboard computers, the rocket was "soft-released" in two stages: first, the hold-down arms released the rocket, and second, as the rocket began to accelerate upwards, it was slowed by tapered metal pins pulled through dies for half a second.[91]
Once the rocket had lifted off, it could not safely settle back down onto the pad if the engines failed. The astronauts considered this one of the tensest moments in riding the Saturn V, for if the rocket did fail to lift off after release they had a low chance of survival given the large amounts of propellant. A fully fueled Saturn V exploding on the pad would have released the energy equivalent of 2 kilotons of TNT (TJ). To improve safety, the Saturn Emergency Detection System (EDS) inhibited engine shutdown for the first 30 seconds of flight. (See Saturn V Instrument Unit)[91]
It took about 12 seconds for the rocket to clear the tower. During this time, it yawed degrees away from the tower to ensure adequate clearance despite adverse winds; this yaw, although small, can be seen in launch photos taken from the east or west. At an altitude of feet (m) the rocket rolled to the correct flight azimuth and then gradually pitched down until 38 seconds after second stage ignition. This pitch program was set according to the prevailing winds during the launch month.[91]
The four outboard engines also tilted toward the outside so that in the event of a premature outboard engine shutdown the remaining engines would thrust through the rocket's center of mass. The Saturn V reached feet per second (m/s) at over 1 mile (1,m) in altitude. Much of the early portion of the flight was spent gaining altitude, with the required velocity coming later. The Saturn V broke the sound barrier at just over 1 minute at an altitude of between and miles ( and km). At this point, shock collars, or condensation clouds, would form around the bottom of the command module and around the top of the second stage.[91]
At about 80 seconds, the rocket experienced maximum dynamic pressure (max q). The dynamic pressure on a rocket varies with air density and the square of relative velocity. Although velocity continues to increase, air density decreases so quickly with altitude that dynamic pressure falls below max q.[91]
Acceleration increased during S-IC flight for three reasons. First, increased acceleration increased the propellant pressure at the engines, increasing the flow rate somewhat. This was the least important factor, though this feedback effect often led to an undesirable thrust oscillation called pogo. Second, as it climbed into thinner air F-1 engine efficiency increased significantly, a property of all rockets. The combined thrust of five engines on the pad was about million pounds-force (33MN), reaching nearly 9million pounds-force (40MN) at altitude. Third, and most importantly, the rocket's mass rapidly decreased.[91]
The propellant in just the S-IC made up about three-quarters of Saturn V's entire launch mass, and it was consumed at 13, kilograms per second (1,,lb/min). Newton's second law of motion states that force is equal to mass multiplied by acceleration, or equivalently that acceleration is equal to force divided by mass, so as the mass decreased (and the force increased somewhat), acceleration rose. Including gravity, launch acceleration was only 114g, i.e., the astronauts felt 114g while the rocket accelerated vertically at 14g. As the rocket rapidly lost mass, total acceleration including gravity increased to nearly 4g at T+ seconds. At this point, the inboard (center) engine was shut down to prevent acceleration from increasing beyond 4g.[91]
When oxidizer or fuel depletion was sensed in the suction assemblies, the remaining four outboard engines were shut down. First stage separation occurred a little less than one second after this to allow for F-1 thrust tail-off. Eight small solid fuel separation motors backed the S-IC from the rest of the vehicle at an altitude of about 42 miles (67km). The first stage continued ballistically to an altitude of about 68 miles (km) and then fell in the Atlantic Ocean about miles (km) downrange.[91]
The engine shutdown procedure was changed for the launch of Skylab to avoid damage to the Apollo Telescope Mount. Rather than shutting down all four outboard engines at once, they were shut down two at a time with a delay to reduce peak acceleration further.[91]
S-II sequence[edit]
After S-IC separation, the S-II second stage burned for 6 minutes and propelled the craft to miles (km) and 15,mph (25,km/h), close to orbital velocity.[92]
For the first two uncrewed launches, eight solid-fuelullage motors ignited for four seconds to accelerate the S-II stage, followed by the ignition of the five J-2 engines. For the first seven crewed Apollo missions only four ullage motors were used on the S-II, and they were eliminated completely for the final four launches. About 30 seconds after first stage separation, the interstage ring dropped from the second stage. This was done with an inertially fixed attitude—orientation around its center of gravity—so that the interstage, only 3feet 3inches (1m) from the outboard J-2 engines, would fall cleanly without hitting them, as the interstage could have potentially damaged two of the J-2 engines if it was attached to the S-IC. Shortly after interstage separation the Launch Escape System was also jettisoned .[92]
If you are not the author of this article and you wish to reproduce material from it in a third party non-RSC publication you must formally request permission using Copyright Clearance Center. Go to our Instructions for using Copyright Clearance Center page for details.
Authors contributing to RSC publications (journal articles, books or book chapters) do not need to formally request permission to reproduce material contained in this article provided that the correct acknowledgement is given with the reproduced material.
Reproduced material should be attributed as follows:
- For reproduction of material from NJC:
Reproduced from Ref. XX with permission from the Centre National de la Recherche Scientifique (CNRS) and The Royal Society of Chemistry. - For reproduction of material from PCCP:
Reproduced from Ref. XX with permission from the PCCP Owner Societies. - For reproduction of material from PPS:
Reproduced from Ref. XX with permission from the European Society for Photobiology, the European Photochemistry Association, and The Royal Society of Chemistry. - For reproduction of material from all other RSC journals and books:
Reproduced from Ref. XX with permission from The Royal Society of Chemistry.
If the material has been adapted instead of reproduced from the original RSC publication "Reproduced from" can be substituted with "Adapted from".
In all cases the Ref. XX is the XXth reference in the list of references.
If you are the author of this article you do not need to formally request permission to reproduce figures, diagrams etc. contained in this article in third party publications or in a thesis or dissertation provided that the correct acknowledgement is given with the reproduced material.
Reproduced material should be attributed as follows:
- For reproduction of material from NJC:
[Original citation] - Reproduced by permission of The Royal Society of Chemistry (RSC) on behalf of the Centre National de la Recherche Scientifique (CNRS) and the RSC - For reproduction of material from PCCP:
[Original citation] - Reproduced by permission of the PCCP Owner Societies - For reproduction of material from PPS:
[Original citation] - Reproduced by permission of The Royal Society of Chemistry (RSC) on behalf of the European Society for Photobiology, the European Photochemistry Association, and RSC - For reproduction of material from all other RSC journals:
[Original citation] - Reproduced by permission of The Royal Society of Chemistry
If you are the author of this article you still need to obtain permission to reproduce the whole article in a third party publication with the exception of reproduction of the whole article in a thesis or dissertation.
Information about reproducing material from RSC articles with different licences is available on our Permission Requests page.
PMC
2. Results and Discussion
General Observations
Table 1 and Table 2 gather values of mean squared error (MSE) for CV and BAC splitting, together with the estimation of uncertainty.
Table 1
Regression results obtained for random CV.
Target | Morgan | MACCSFP | ||||
---|---|---|---|---|---|---|
MSE | Dropout MSE | Uncertainty | MSE | Dropout MSE | Uncertainty | |
5-HT1A | ± | ± | ± | ± | ± | ± |
ACM1 | ± | ± | ± | ± | ± | ± |
D2 | ± | ± | ± | ± | ± | ± |
5-HT2A | ± | ± | ± | ± | ± | ± |
5-HT2C | ± | ± | ± | ± | ± | ± |
A1 | ± | ± | ± | ± | ± | ± |
A2A | ± | ± | ± | ± | ± | ± |
H3 | ± | ± | ± | ± | ± | ± |
5-HT7 | ± | ± | ± | ± | ± | ± |
5-HT6 | ± | ± | ± | ± | ± | ± |
MT1A | ± | ± | ± | ± | ± | ± |
MT1B | ± | ± | ± | ± | ± | ± |
CB1 | ± | ± | ± | ± | ± | ± |
MOR | ± | ± | ± | ± | ± | ± |
DOR | ± | ± | ± | ± | ± | ± |
KOR | ± | ± | ± | ± | ± | ± |
CB2 | ± | ± | ± | ± | ± | ± |
MC4 | ± | ± | ± | ± | ± | ± |
mGluR5 | ± | ± | ± | ± | ± | ± |
CCR2 | ± | ± | ± | ± | ± | ± |
B1 | ± | ± | ± | ± | ± | ± |
MC5 | ± | ± | ± | ± | ± | ± |
MC3 | ± | ± | ± | ± | ± | ± |
OX2R | ± | ± | ± | ± | ± | ± |
OX1R | ± | ± | ± | ± | ± | ± |
Table 2
Regression results obtained for BAC.
Target | Morgan FP | MACCSFP | ||||
---|---|---|---|---|---|---|
MSE | Dropout MSE | Uncertainty | MSE | Dropout MSE | Uncertainty | |
5-HT1A | ± | ± | ± | ± | ± | ± |
ACM1 | ± | ± | ± | ± | ± | ± |
D2 | ± | ± | ± | ± | ± | ± |
5-HT2A | ± | ± | ± | ± | ± | ± |
5-HT2C | ± | ± | ± | ± | ± | ± |
A1 | ± | ± | ± | ± | ± | ± |
A2A | ± | ± | ± | ± | ± | ± |
H3 | ± | ± | ± | ± | ± | ± |
5-HT7 | ± | ± | ± | ± | ± | ± |
5-HT6 | ± | ± | ± | ± | ± | ± |
MT1A | ± | ± | ± | ± | ± | ± |
MT1B | ± | ± | ± | ± | ± | ± |
CB1 | ± | ± | ± | ± | ± | ± |
MOR | ± | ± | ± | ± | ± | ± |
DOR | ± | ± | ± | ± | ± | ± |
KOR | ± | ± | ± | ± | ± | ± |
CB2 | ± | ± | ± | ± | ± | ± |
MC4 | ± | ± | ± | ± | ± | ± |
mGluR5 | ± | ± | ± | ± | ± | ± |
CCR2 | ± | ± | ± | ± | ± | ± |
B1 | ± | ± | ± | ± | ± | ± |
MC5 | ± | ± | ± | ± | ± | ± |
MC3 | ± | ± | ± | ± | ± | ± |
OX2R | ± | ± | ± | ± | ± | ± |
OX1R | ± | ± | ± | ± | ± | ± |
The results gathered in Table 1 and Table 2 show that in general, MSE values were much higher for BAC splitting than random CV, which is related to increased task simplicity when compounds are divided into folds randomly [35]. In BAC splitting, the compounds from the test set are supposed to be structurally dissimilar to those that are present in the training set; therefore, via this approach we can evaluate the true ability of ML models to assess compounds covering broad chemical space. Nevertheless, using such an approach for ML methods evaluation is always related to worse performance, as CV-based output provides overoptimistic results (the compounds from the test set resemble examples from the training set, so the evaluation task is relatively simple) that are not reflected in real application of such models.
Interestingly, MSE values obtained for MACCSFP are higher in both CV and BAC splitting in comparison to hashed Morgan FP representation. The difference is higher for BAC splitting, but it is related to higher MSE values for these experiments.
Another consistent observation is that MSE is higher than dropout MSE, which means that the non-deterministic MSE is lower than its deterministic equivalent. It can be explained in such a way, that multiple drawing of dropouts masks is identical to the prediction of the network committee, which usually is characterized by slightly better results.
Our last observation is connected with uncertainty evaluation. It also reaches higher values for BAC experiments in comparison to CV, while on the other hand, when different compound representations are compared, uncertainty values are higher for MACCSFP in comparison to Morgan FP.
When the results are examined from the target point of view, the highest error rate is observed for ACM1, mGluR5, ACM1 and ACM2 for both representations and splitting approaches and the lowest for D2 and MC3. In general, smaller datasets led to worse prediction efficiency.
Analysis of Uncertainties, Errors and Compound Similarities
The visualization of dependencies between the regression error, similarity to the training set (calculated for Morgan FP and with the use of Tanimoto coefficient) and uncertainty was performed (Figure 1, Supporting Information File S1).
Visual analysis of dependencies between mean squared error (MSE), prediction uncertainty and compound similarity for adenosine A1 receptor. (a) MSE vs. similarity for Morgan FP in CV; (b) uncertainty vs. similarity for Morgan FP in CV (c) MSE vs. uncertainty for Morgan FP in CV; (d) MSE vs. similarity for Morgan FP in BAC; (e) uncertainty vs. similarity for Morgan FP in BAC; (f) MSE vs. uncertainty for Morgan FP in BAC; (g) MSE vs. similarity for MACCSFP in CV; (h) uncertainty vs. similarity for MACCSFP in CV (i) MSE vs. uncertainty for MACCSFP in CV; (j) MSE vs. similarity for MACCSFP in BAC; (k) uncertainty vs. similarity for MACCSFP in BAC; (l) MSE vs. uncertainty for MACCSFP in BAC.
The first observation coming from Figure 1 is that there is no significant difference between results obtained for two representation usedthe only qualitative and strong indicated differentiation is the uncertainty vs. similarity dependence for random CV, which is spread over greater area for Morgan FP than MACCSFP. For this dependency it is also visible that the data points are placed differently when random CV vs. BAC splitting is consideredfor random CV, the datapoints are concentrated closer to higher values of similarity coefficients, whereas for BAC they are spreading from the corner with lower similarity and uncertainty values. The highest concentration of datapoints in lower values of both parameters considered (MSE and uncertainty) is also observed for MACCSFP and random CV; for other combinations of dataset splitting approach and representation the datapoints cover much broader space of the respective chart although and MSE is more concentrated parameter than uncertainty, which adopts quite broad range of values. MSE vs. similarity charts also much more depended on the splitting approach than the compound representation and the highest concentration of points is shifted towards higher similarity values for random CV than for BAC.
Another type of analysis involved the examination of relationships between the number of different activity values reported and average prediction uncertainty (Figure 2, Supporting Information File S2). In the case, no box is presented on the chart, only one compound was reported for particular number of activity values. Activity range is shown by lines, box size refers to first and last quartile and orange line to median activity value. The results show that there is no direct relationship between the number of activity values provided for particular compound and uncertainty of predictions obtained for them, for both random CV and BAC. No direct conclusion that increasing number of activity values reported led to higher uncertainty can be drawn.
Analysis of dependency between prediction uncertainty and number of activity values provided for particular compound in the ChEMBL database for dopamine D2 ligands. (a) for Morgan FP in CV experiments; (b) for MACCFP in CV experiments; (c) for Morgan FP in BAC experiments; (d) for Morgan FP in BAC experiments.
Last type of analysis involved the examination of correlation between the standard deviation of activity values reported for given compound and prediction uncertainty (Figure 3, Supporting Information File S3).
Analysis of dependency between prediction uncertainty and standard deviation of activity values provided for particular compound in the ChEMBL database for adenosine A1 ligands. (a) for Morgan FP in CV experiments; (b) for MACCFP in CV experiments; (c) for Morgan FP in BAC experiments; (d) for Morgan FP in BAC experiments.
The first observation coming from Figure 4 is that the consistency in data in training set (standard deviation of activity values equal to zero) is not related to clear and certain predictions for given compound and wide range of uncertainty is assigned to compounds with standard deviation of activity values equal to zero. Further, there is no correlation between standard deviation and uncertainty of predictions and even for compounds with wide range of activity values reported, predictions with low uncertainty can be obtained.
Compounds Ranking
In this experiment, we sorted compounds using particular strategy and the results were compared with the sorting based on true activities. The baseline model performs sorting only on the basis of prediction of a model, remaining strategies use also information about model uncertainty in various ways. It was indicated that using information about uncertainty in general improves sorting efficiency.
For the ranking strategies, we will assume that is the predicted bioactivity (in terms of affinity valuesKi) and ui is the prediction uncertainty. We will denote as output of ranking function, meaning the lower the R value, the higher in our ranking the compound is.
The following ranking strategies were used:
Baselineonly prediction of a model is taken into account
Addto model prediction, information about uncertainty is added directly; the less uncertain the model is about the sample, the better
Scalethe uncertainty estimation is normalized to fit the range of [0,1]) and used to scale the prediction
where is a normalized uncertainty based on the measures for the whole test set.
Add scaledthe uncertainty estimation is normalized to fit into [0,1] and added directly to the prediction
Sum scaledboth prediction of a model and its uncertainty are normalized and then summed up
where is a normalized prediction based on the predictions over the whole dataset.
Comb »linear combination of prediction and uncertainty with the » coefficient (various » values were tested).
The results are presented in the form of the so-called precision at top 10% , which means that the compounds are sorted on the basis of their activity (two lists are prepared: based on true activity and based on the predicted values of activity parameters). Then, the 10% of top scored compounds from the list of the most active compounds is picked up and it is cross-checked with the list of the 10% of top scored compounds on the basis of predicted activity. The percentage of overlapping compounds between these two lists for different strategies for BAC splitting for example targets is gathered in Figure 4.
We can notice that the results and prediction effectiveness strongly depend both on the target, as well as compound representation. For all targets presented in Figure 4 Morgan FP appeared to be more effective representation. The differences in precision between different compound representations also vary for various targetsfrom slight differences for 5-HT2C, via a ~ difference for M1, A1, H3 and 5-HT7, to up to difference for 5-HT1A. On the other hand, the differences related to various compound representations were higher than differences related to application of different approaches. When information on uncertainty is added, the precision values averaged over all targets considered revealed that for both compound representations _add approach was the best. Nevertheless, in both cases, the improvement in comparison to baseline was relatively low and for MorganFP and MACCSFP, respectively when averaged values for all targets are taken into account.
However, considering particular cases separately, there was an approach that improved the accuracy of ML predictions in comparison to baseline; there were examples where these improvement was quite significant. For example, for D2 and H3 ligands, precision at top 10% was higher by ~ when _sum_scaled approach is compared to baseline (for Morgan FP). _sum_scaled approach gave the highest improvement over baseline for A2A, for MACCSFP representation (~).
In order to examine the influence of incorporation of uncertainty into ML models, the heat maps were prepared comparing the precision at top 10% for baseline and other approaches (Figure 5).
Figure 5 clearly show that in the majority of cases incorporation of information about prediction uncertainty improved efficiency of predictions of ML models (indicated by pink and red cells on heat maps). Nevertheless, the results strongly depend on target and compound representation. For M1, A2A and 5-HT6, strong improvement is observed for MACCSFP; for Morgan FP, it was D2, A2A and H3 that led to the highest improvement. This effect (for both representations is observed mainly for _add, _add_scaled and _sum_scaled approaches. On the other hand, the _sum_scaled approach was the only one for which the worsening of the results was observed for some targets (M1, A1 and 5-HT6 for Morgan FP and M1 and 5-HT2C for MACCSFP).
Detection of Potential Errors in Bioactivity Databases
The developed methodology was used for detection of potential errors in the ChEMBL database. First of all, for all targets considered, the MSE of activity prediction together with uncertainties were calculated for the test set (Figure 6).
On the basis of these data, the suspected data points were indicated; they were defined as those for which the MSE was in the 95 percentile (and higher) and uncertainty on the 5th percentile (and higher).
Examples of such compoundstogether with the true activities reported and activities of 10 most similar compoundsare presented below (Figure 7).
The provided examples of dopamine D2 ligands prove that the prediction uncertainty is not correlated with the standard deviation of activity values provided in activity databases. For ligand CHEMBL, there were 8 Ki values towards D2 receptor reported, ranging from nM to nM (with the average Ki equal to nM) and standard deviation of nM. The predicted Ki for this compound is however much lower than the actual affinity values and is equal to nM which is expressed also by high uncertainty factor (). The relatively low value of predicted Ki is a result of activities of similar compounds present in the dataset. Figure 7 presents only selected examples, but even among them can be found compounds with much lower Ki than actual average Ki, such as CHEMBL, for which two Ki values are reported (37 and nM). On the other hand, there is compound CHEMBL, for which only one Ki value is available ( nM). Although for this compound, the standard deviation of Ki values is equal to zero, the prediction uncertainty is similar to the uncertainty determined for CHEMBL () and the predicted Ki for this compound is equal to nM. In this case, the activity of similar compounds is in narrower range, as the most active CHEMBL has affinity of nM, but there is also CHEMBL, whose Ki is equal to 21 nM.
What’s New in the 3D Exploration 1.833 serial key or number?
Screen Shot

System Requirements for 3D Exploration 1.833 serial key or number
- First, download the 3D Exploration 1.833 serial key or number
-
You can download its setup from given links: